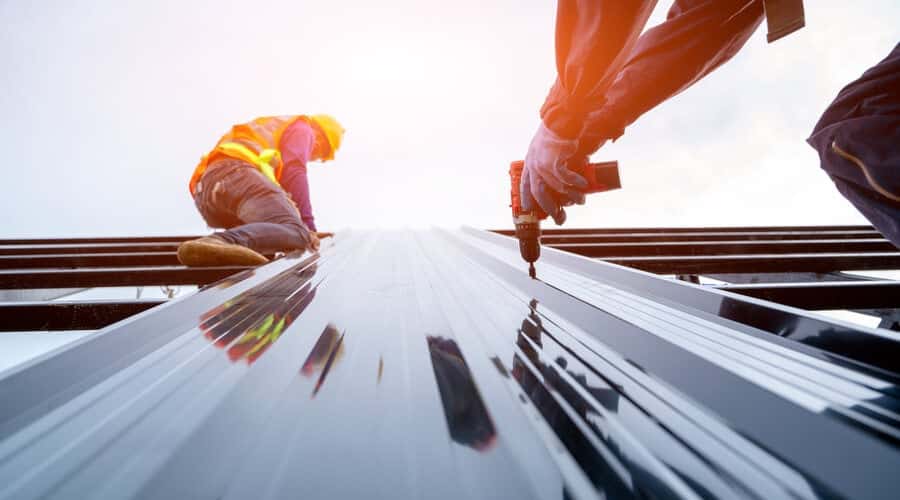
In this article, we look at what a QMP is and outline its key components.
Delivering high-quality results is a fundamental priority for construction projects. However, managing quality outputs with multiple subcontractors on a large scale project is easier said than done. Without a comprehensive QMP in place, a high quality end result is harder to achieve. So, what is a QMP and why is it so important?
Read on for more on QMP meaning.
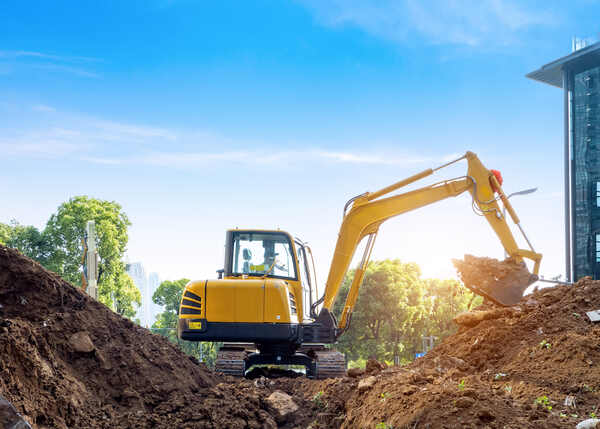
Builder Assist have developed comprehensive Quality Management Plan templates specific to all trades. From Excavation to Roofing, Rough-in to Carpet and everything in between.
Curious about QMP meaning? What is a QMP?
A QMP is a Quality Management Plan. It describes a construction project’s policies, procedures and guidelines related to quality management.
A QMP ensures workmanship is to the highest standard. In addition, it ensures the efficiency of internal processes.
A Quality Management Plan outlines the activities and resources necessary to reach quality objectives consistently and effectively.
When the QMP is followed, customer satisfaction and loyalty increases, and naturally, so does a brand’s reputation and referrals!
So, you now know QMP meaning. What are the main components?
What are the main components of a Quality Management Plan?
Every construction project is different, but a QMP framework remains largely the same.
The four main components that make up a Quality Management Plan are:
- Quality Planning
- Quality Assurance
- Quality Control
- Continuous Improvement
We’ve broken down each component to give you an understanding of its importance.
Quality Planning
This first phase of a QMP defines the standard of quality for the project.
Additionally, it outlines how quality management is performed. It describes:
- Any applicable legal standards or internal business standards that are required for the project.
- The expectation of your client/customer and their main project objective/s when it comes to quality.
- How the success of the project is measured, both from a tangible, product perspective, and the effectiveness of processes across the life of the project.
- Roles and responsibilities of key personnel regarding quality management. This could include roles like Quality Assurance Advisor, Project Manager, Site Supervisor and an appointment Quality Management Committee.
- An outline of the processes that are followed to achieve the identified standard of quality. This details the quality control measures that are used, how quality assurance is performed, and an overview of how the project and key personnel ensure continuous improvement is actioned throughout the project.
Quality Assurance
Quality Assurance (QA) is carried out across a project's lifespan. It's implemented for a number of reasons.
Primarily, QA ensures the project moves forward according to the agreed processes and procedures.
In addition, effective QA provides assurance to the client that the project is delivered to the expected standard.
QA involves pre-planned reviews and audits of processes and deliverables. This identifies non-compliance and opportunities for improvement.
Reviews and audits are documented and stored, and then revisited if necessary.
Quality Control
Quality control ensures products and materials are compliant.
In addition, it ensures products and materials meet the quality standard agreed upon by the client and the project manager.
Importantly, Quality Control ensures workers, management and all staff on site adhere to the project's quality standards.
Continuous Improvement
The last, but certainly not the least important component of a Quality Management Plan is seeking opportunities for continuous improvement.
Continuous improvement is applicable across all aspects of a project. It identifies processes, materials and/or procedures to be improved upon to increase efficiency and quality.
Continuous improvement also works to find opportunities to refine the quality management plan itself.
Without a dedicated continuous improvement process, businesses may struggle to move forward to meet a client’s quality expectations.
Quality Management Plan Template
Builder Assist have developed comprehensive Quality Management Plan templates specific to all trades.
From Excavation to Roofing, Rough in to Carpet and everything in between.
There’s a Quality Management Plan suitable for your trade, ready to download today.
Additionally, our templates are designed to guide personnel through quality management and assurance activities for every project.
You can view and download your own Quality Management Plan specific to your trade. Easy.